The comfort and range challenges posed by BEV´s (Battery Electric Vehicles) are driving demand for higher power efficiency, noise reduction and general light-weighting of all vehicle components. The car seat is one area that will evolve quickly due to changing trends and the need to operate quietly for passenger comfort, operate longer, and be fully maneuverable. Moreover, seats have to provide many additional functions, which increases their weight and the adjusting mechanism’s rotation speed becomes faster.
Vehicle seat designers are challenged to meet the drivers' demands for a smoother, quieter, and more comfortable experience – and they expect it to last.
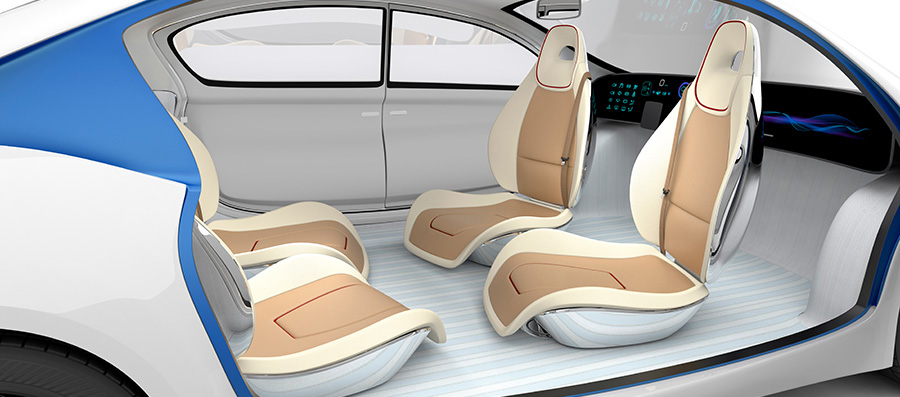
At the end of the day, an automotive interior connects people to their vehicles, and seat designers must accomplish all of this while minimizing costs and fulfilling the even more stringent regulations in regards of sustainability. The importance of developing increasingly flexible and secure seats cannot be overlooked, all while reducing component weight and minimizing noise.
It is time to think small
What many engineers do not realize is that bearings often determine other components, including the housing, shaft, and support structures, and are instrumental to a properly fit seat. These small components can cause a chain reaction that results in unforeseen consequences.
Customized Solution Engineering
Such car seat mechanism designs require a high level of tribology expertise, engineering design and creativity from a multi-disciplinary team to generate new design concepts, test them and converge towards an optimized solution.
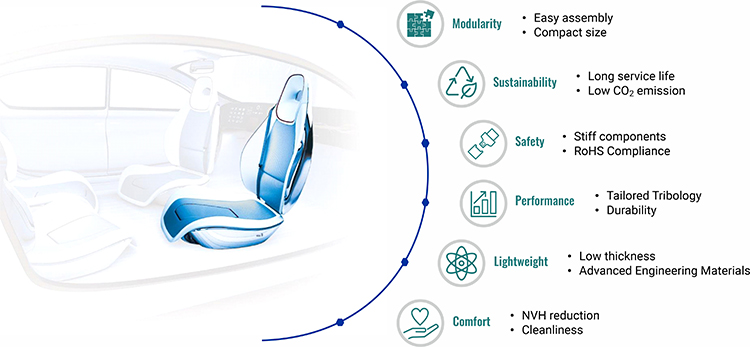
From assembly, packaging, and logistics to technical support, GGB expands beyond traditional surface engineered solutions to create something that is uniquely adapted for your requirements. GGB seat bearings and surface solutions not only meet strict criteria for the design, function, and CO2 emissions, they also help make for safer vehicles with better fuel economy.